Contact us to know how Simulation can help you improve your product quality and reduce prototype costs
Improve product quality and reduce prototype costs by using Finite Element Analysis. Here are some of the benefits of Simulation
- Subject your designs to real-world conditions to raise product quality while reducing prototyping and physical testing costs.
- Enhanced design and early evaluation of critical design parameters
- Safe simulation of potentially dangerous, destructive, or impractical load conditions and failure modes.
- The simultaneous calculation and visual representation of a wide variety of physical parameters such as stress or temperature, enabling the designer to rapidly analyze performance and possible modifications.
- Optimizing your design by reducing weight and material without compromising the quality of the product before fabrication.
- Easily spot any vulnerability in design with the detailed visualizations FEA produces, then use the new data to make a new design.
- Relatively low investment and rapid calculation time for most applications.
- Maximize performance through material selection and cost-efficiency.
- Reduced R&D and development costs.
- Calculate the life-cycle of your design
Static analysis
Static relates to the time component of the analysis. So it means simply that an analysis that is static takes the assumption that your system doesn’t depend on time.
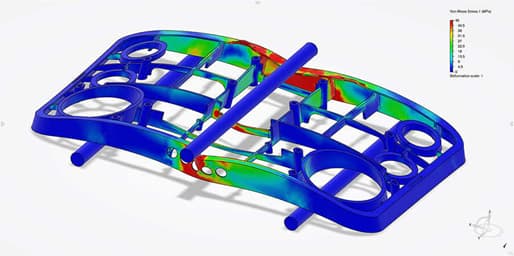
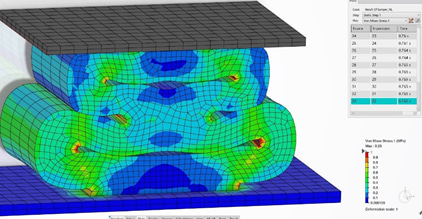
Non-Linear: Perform non-linear analysis using the hyperelastic, viscoelastic materials
We perform highly non-linear analysis when the structure subjected to non-linear effects as follows,
- Material non-linearity (i.e. hyper-elastic, viscoelastic material)
- Geometrical nonlinearity (i.e. large deformation)
- Contact non-linearity (Restriction in DOF)
Dynamic analysis: Perform the impact analysis to check the structure behavior
We perform dynamic analysis to check the structure behavior It is useful to consider vehicle impact speeds to describe the different physics involved and that we wish to simulate.
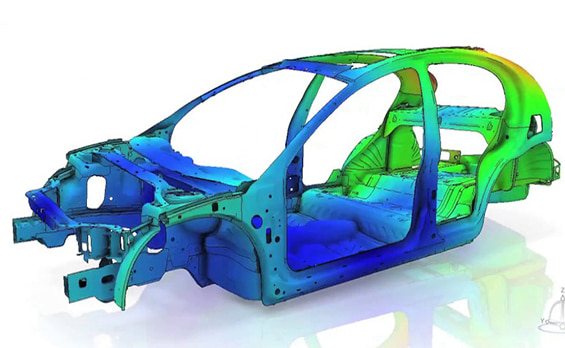
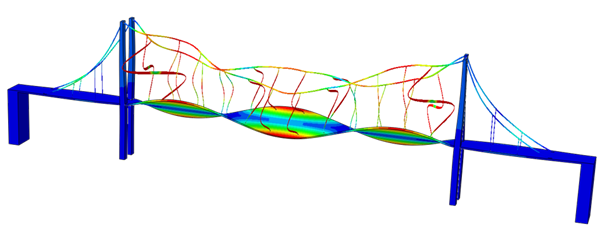
Frequency- Calculating the resonance frequency of the structure to avoid the structure collapse
Modal analysis (Frequency) helps to determine the modes of vibrations and the frequencies at which those modes are triggered. Calculating the resonance frequency of the structure to avoid the structure collapse.
Vibration Analysis
A Random Vibration Analysis (RVA) is used to calculate the system’s structural response to a spectrum of random excitations and non-deterministic loads. Examples of non-deterministic loads include loads generated on a wheel traveling over a rough road or random structural vibrations on the airframe of a helicopter. RVA is conducted in the frequency domain and is usually performed over a large range of frequencies
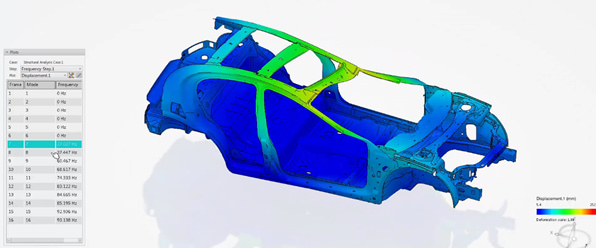
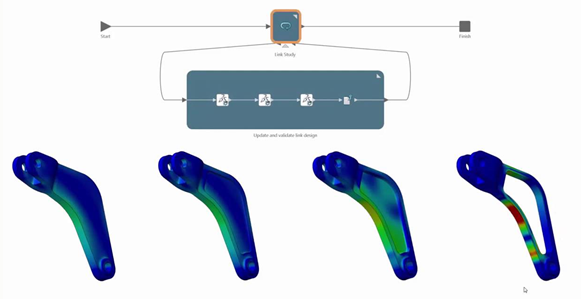
Design Optimization: Reduce the material cost without compromising the product strength.
Design optimization is one of the largest advantages of finite element analysis (FEA). Through gaining a strong understanding of the performance of your product with FEA you can reduce material, prevent stress concentrations, remove bottlenecks, and attain desirable performance attributes.
Flow Analysis:
- Wind tunnel tests provide the necessary design pressure measurements in the use of the dynamic analysis and control of tall buildings.
- And to calculate lift and drag force on your design
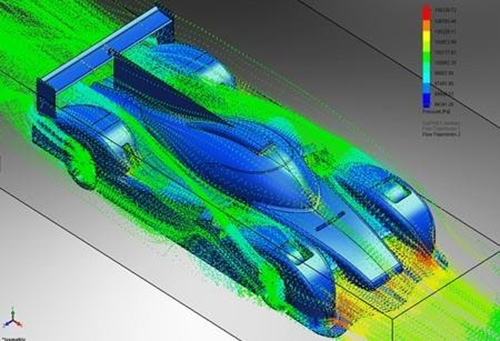
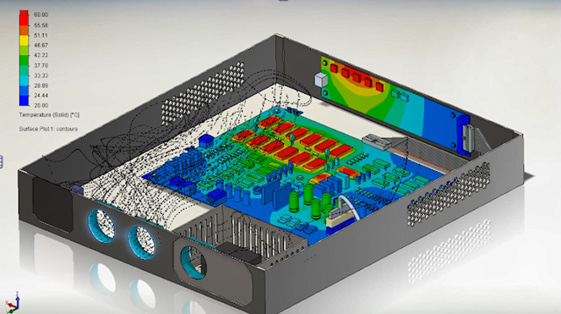
Electronic cooling- Calculate the heat dissipation of heat inside the enclosure to avoid product failure.
We do simulate the heat introduced to a simulation by a battery or other electronics components, along with the cooling effects of fans. This workflow enables you to investigate the battery’s Joule heating behavior.
Thermal Analysis
Heat transfer can also be computed via the finite element method with the added advantage that the thermally induced deformation and stresses can be easily determined and combined with other types of analyses.
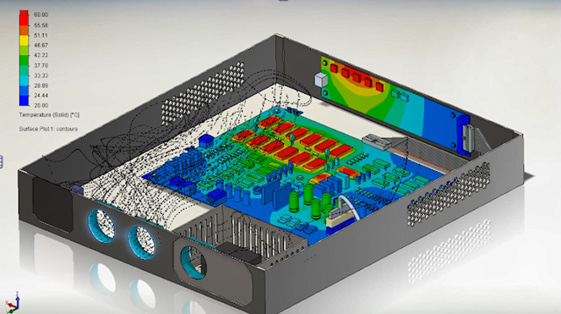